Operations Management: A Comprehensive Overview
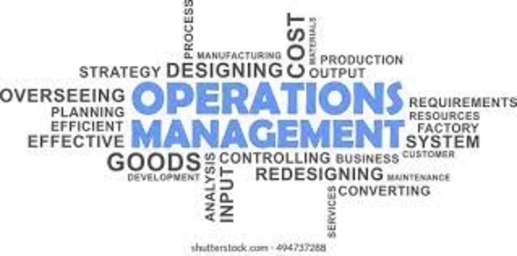
Operations Management: A Comprehensive Overview
Operations Management (OM) refers to the administration of business practices aimed at maximizing efficiency within an organization. It involves managing the processes that convert inputs (materials, labor, capital) into outputs (goods and services) to ensure they are produced in the most efficient and cost-effective way. This discipline is vital for ensuring the smooth functioning of businesses and achieving strategic goals related to quality, profitability, and customer satisfaction.
Key Components of Operations Management
-
Process Design and Management:
- Involves designing efficient processes to achieve productivity and quality goals.
- Includes decisions related to workflow, product design, and resource allocation.
- Focus on streamlining operations by identifying bottlenecks or inefficiencies.
-
Supply Chain Management (SCM):
- The coordination and integration of supply chain activities to deliver goods/services efficiently.
- Encompasses sourcing raw materials, managing inventory, production, and distribution.
- Tools for effective SCM:
- Just-in-Time (JIT): Minimizing inventory levels while meeting demand.
- Lean Manufacturing: Reducing waste while maintaining quality and value.
-
Capacity Planning:
- Ensuring that the organization has sufficient resources (equipment, facilities, labor) to meet production demands.
- Balancing underutilization of resources (leading to waste) and overutilization (causing delays and quality issues).
-
Quality Management:
- Includes maintaining product/service standards to meet or exceed customer expectations.
- Frameworks and techniques:
- Total Quality Management (TQM): Organizational-wide efforts to continuously improve quality.
- Six Sigma: Data-driven methodology aimed at reducing defects and variations in processes.
- ISO 9001 Certification: Ensuring quality standards are met in products or services.
-
Inventory Control:
- Balancing inventory levels to prevent stockouts or overstocking.
- Techniques include:
- Economic Order Quantity (EOQ): Determining the optimal order size.
- ABC Analysis: Categorizing inventory based on importance (e.g., high-value vs. low-value items).
-
Production and Operations Scheduling:
- Planning the production schedule to ensure timely delivery of products/services.
- Tools include:
- Gantt Charts: Visual representation of a schedule.
- Critical Path Analysis (CPA): Identifying critical steps and ensuring they’re completed on time.
-
Cost Management:
- Ensuring operational costs (e.g., labor, raw materials, logistics) are effectively managed to maximize profits.
- Tools:
- Activity-Based Costing (ABC): Assigning costs based on specific activities or processes.
-
Technology and Automation in Operations:
- Leveraging advancements such as robotics, artificial intelligence (AI), and machine learning to optimize processes.
- Examples:
- Automated inventory systems.
- AI-driven demand forecasting.
Tools and Methods in Operations Management
- Kaizen (Continuous Improvement): A philosophy focused on small, continuous changes to improve efficiency and quality.
- Value Stream Mapping: A visual tool to analyze and improve workflows.
- PERT (Program Evaluation and Review Technique): For project scheduling and coordination.
- ERP (Enterprise Resource Planning) Systems: Integrating core business processes into a unified system (e.g., SAP, Oracle).
Importance of Operations Management
-
Efficiency and Productivity:
- Ensures optimal use of resources to minimize costs and maximize output.
-
Customer Satisfaction:
- Timely delivery of products/services with consistent quality enhances trust and reliability.
-
Cost Reduction:
- Effective inventory management, lean practices, and waste reduction lead to cost savings.
-
Competitive Advantage:
- Efficient operations enable faster response to market changes and customer demands.
-
Sustainability:
- Operations management emphasizes reducing waste, optimizing energy use, and adopting eco-friendly practices.
Operations Management in Practice
-
Manufacturing Sector:
- Operations management focuses on production planning, equipment maintenance, and assembly line efficiency.
- Example: Toyota employs lean manufacturing and JIT systems to reduce waste and improve productivity.
-
Service Sector:
- Includes process optimization in areas like healthcare, retail, and hospitality.
- Example: Amazon uses advanced supply chain and logistics strategies to ensure rapid order fulfillment.
-
Small and Medium Enterprises (SMEs):
- Operations management helps SMEs optimize limited resources, ensuring sustainable growth.
- Example: A local bakery managing inventory for fresh ingredients while minimizing waste.
Skills Developed Through Operations Management Education
- Analytical Skills:
- Identifying inefficiencies and optimizing processes.
- Problem-Solving:
- Designing solutions for challenges like delays, excess inventory, or supply chain disruptions.
- Leadership and Team Management:
- Leading teams to execute operational strategies effectively.
- Project Management:
- Overseeing complex projects, from scheduling to delivery.
- Technical Proficiency:
- Using tools like ERP systems, inventory software, and project scheduling applications.
Career Opportunities in Operations Management
Graduates in Operations Management can pursue diverse career paths across industries:
- Operations Manager:
- Oversees daily operations, optimizing workflow and managing teams.
- Supply Chain Manager:
- Manages logistics, procurement, and supplier relationships.
- Production Manager:
- Supervises manufacturing processes to ensure timely delivery.
- Quality Control Manager:
- Ensures products/services meet quality and regulatory standards.
- Logistics Manager:
- Coordinates transportation and distribution networks.
- Process Improvement Specialist:
- Analyzes and redesigns business processes for efficiency.
Operations Management Education in Canada
Canadian universities offer cutting-edge courses in Operations Management, blending theory with real-world applications. These programs often cover SCM, process optimization, and technology integration.
- Rotman School of Management (University of Toronto):
- Offers courses on global operations strategy, supply chain design, and process optimization.
- Sauder School of Business (University of British Columbia):
- Focuses on logistics, quality management, and business analytics.
- Schulich School of Business (York University):
- Includes studies in operations design, innovation, and automation.
- HEC Montréal:
- Specializes in sustainable operations and global logistics.
- DeGroote School of Business (McMaster University):
- Hosts courses tailored to SCM, project management, and ERP systems.
Conclusion
Operations Management is a vital discipline that ensures businesses run efficiently, producing quality goods and services while controlling costs. With the rise of technological innovations, global supply chains, and customer expectations, professionals in this field play a crucial role in maintaining competitive advantages. By studying operations management, individuals gain the skills to design and optimize processes, enabling organizations to function successfully in dynamic business environments. Canadian institutions are leaders in training students for this critical field, providing a mix of theoretical frameworks and practical applications for excelling in their careers.